Comprehensive Guide to Tooling for Injection Molding
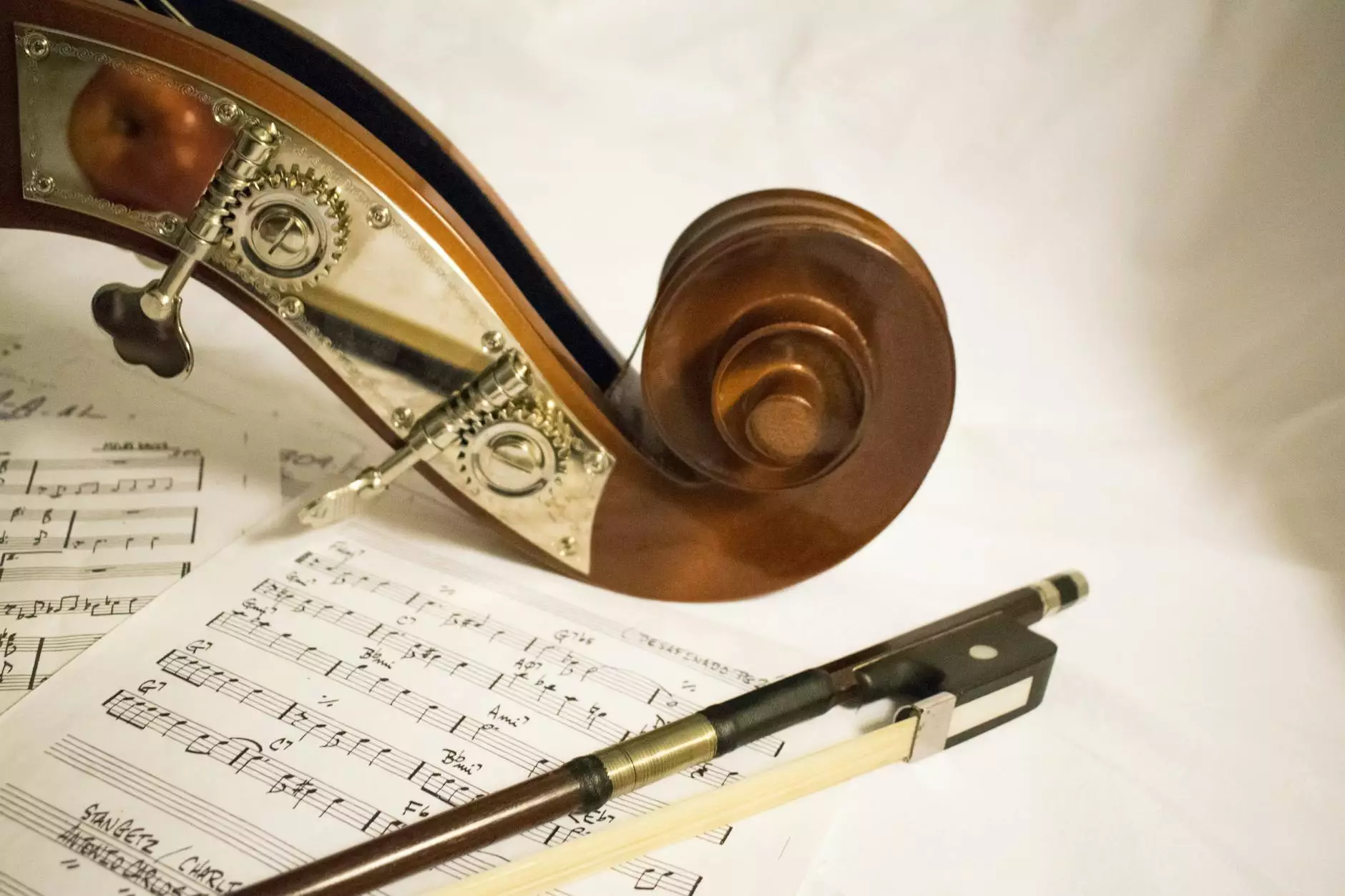
In the world of manufacturing, precision is key. One of the most critical aspects of achieving this precision, particularly in the production of complex parts, is tooling for injection molding. This guide delves deeply into the importance, techniques, and innovations surrounding tooling in the injection molding process.
Understanding Injection Molding
Injection molding is a manufacturing process for producing parts by injecting material into a mold. It is widely used for manufacturing plastic parts, but its applications extend into metal as well, especially when combined with specialist techniques like metal injection molding (MIM).
The Importance of Tooling in Injection Molding
Tooling is a term that encompasses the various molds, dies, and equipment used to shape materials into finished products. The significance of effective tooling for injection molding cannot be overstated:
- Precision and Accuracy: Proper tooling ensures that each part produced meets stringent specifications.
- Efficiency: Well-designed tools enable faster production times, reducing overall manufacturing costs.
- Quality Control: Good tooling allows for consistency in the quality of finished products, which is crucial for customer satisfaction.
Types of Tooling for Injection Molding
There are various types of tooling utilized in the injection molding process, each tailored to specific needs:
Single Cavity Molds
These molds produce a single part per cycle. Ideal for low-volume production, single cavity molds are simpler to design and manufacture.
Multi-Cavity Molds
Multi-cavity molds contain several cavities that produce multiple parts in one cycle. They are cost-effective for high volume production.
Family Molds
Family molds can produce different parts simultaneously, making them suitable for products that require related components.
Hot Runner Molds
Hot runner systems keep the plastic in a molten state, reducing waste and improving cycle times.
Key Considerations in Tool Design
The design of tooling for injection molding involves several critical considerations that can dramatically affect production outcomes:
- Material Selection: Choosing the right materials for the mold itself is essential. Materials must withstand high pressures and temperatures.
- Cooling Systems: Effective cooling mechanisms help enhance cycle times and improve the quality of the final product.
- Mold Geometry: The geometry of the mold must facilitate easy part removal while ensuring that the part’s detail is preserved.
Manufacturing Processes for Tooling
The processes involved in manufacturing tooling for injection molding are diverse.
1. CNC Machining
CNC machining is a vital part of tooling production that allows for high precision in cutting and shaping materials.
2. EDM (Electrical Discharge Machining)
EDM is essential for achieving intricate shapes and features in hard materials, improving tooling capabilities.
3. 3D Printing
3D printing technology is revolutionizing tooling production by allowing for rapid prototyping and the production of complex geometries that were previously difficult to achieve.
Benefits of High-Quality Tooling
Investing in high-quality tooling for injection molding yields numerous benefits:
- Reduced Production Costs: High-quality tools lead to fewer defects and lower scrap rates.
- Shorter Lead Times: Well-engineered tools can reduce the time required to produce parts, accelerating time-to-market.
- Enhanced Product Features: Advanced tooling can enable more complex part features, expanding design possibilities.
Challenges in Tooling for Injection Molding
Despite its benefits, tooling for injection molding can present challenges:
- Investment Costs: High-quality tooling requires a significant upfront investment, which can be a barrier for small businesses.
- Maintenance Requirements: Continuous use of tooling necessitates regular maintenance to ensure longevity and operational effectiveness.
- Design Complexity: Creating and producing complex molds can be time-consuming and requires skilled personnel.
Future Trends in Tooling for Injection Molding
The manufacturing industry is constantly evolving. Here are some trends shaping the future of tooling for injection molding:
- Smart Manufacturing: The incorporation of sensors and IoT technology is helping manufacturers monitor tooling performance in real time.
- Sustainability: As businesses become more eco-conscious, there is a push for tooling that minimizes waste and energy consumption.
- Advanced Materials: The development of new materials for both tooling and molded parts is leading to enhancements in performance and sustainability.
Why Choose DeepMould for Tooling Solutions?
At deepmould.net, we specialize in providing top-notch tooling for injection molding. Here’s why you should choose us:
- Expertise: Our team consists of highly skilled engineers and designers who understand the intricacies of tooling.
- Quality Assurance: We adhere to rigorous quality control processes to ensure that every tool we produce meets the highest standards.
- Customized Solutions: We provide tailored tooling solutions that meet the specific needs of your production process.
- Cutting-Edge Technology: We leverage the latest technology in tooling design and production to deliver efficient and innovative solutions.
Conclusion
In summary, tooling for injection molding is an essential aspect of modern manufacturing that can greatly influence production efficiency and product quality. Techniques, designs, and materials for tooling are continuously evolving, making it crucial for businesses to stay informed and adaptable. Partnering with experts like those at deepmould.net can ensure that you are using the best practices and technologies available. Embrace the future of manufacturing with adept tooling solutions that place high value on precision, efficiency, and quality.
As the industry progresses, those who invest in superior tooling for injection molding will undoubtedly find themselves at a competitive advantage. Whether you are a small business or a large operation, understanding and improving your tooling process is vital for sustainable growth and success.