Maximizing **UV Ink Adhesion**: A Comprehensive Guide
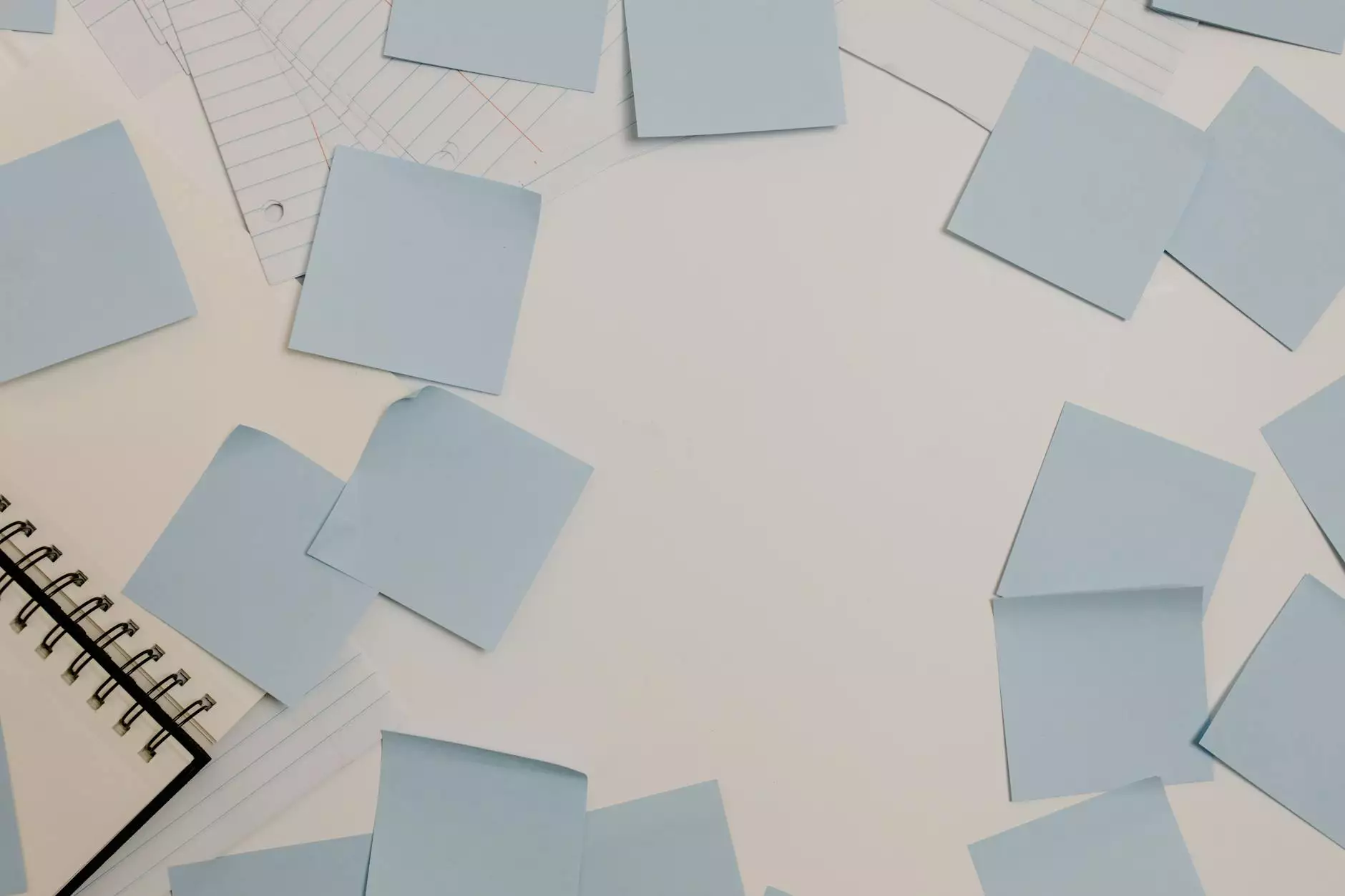
Understanding UV Ink Adhesion
UV ink adhesion is a critical factor in the quality and durability of printed materials. When UV inks are cured by ultraviolet light, they bond to the surface of the substrate, creating vibrant colors and sharp details. However, achieving optimal adhesion requires understanding various factors that influence it.
In this article, we will delve into the intricacies of UV ink adhesion, including its significance in the printing process, methods to enhance adhesion, and the challenges faced in achieving the best results.
The Importance of UV Ink Adhesion in Printing Services
In the world of printing, UV ink adhesion is paramount because it affects:
- Print Quality: Good adhesion ensures that colors remain vibrant and the details sharp.
- Durability: Adhesion affects the lifespan of prints, especially regarding wear and exposure to elements.
- Substrate Compatibility: Different materials require unique adhesion strategies to achieve optimal results.
Businesses like bostonindustrialsolutions.com understand these factors, providing robust solutions in their printing services by ensuring excellent ink adhesion in all projects.
Factors Affecting UV Ink Adhesion
Several elements influence the level of adhesion achieved with UV inks. Understanding these factors is essential for printers looking to optimize their processes:
1. Substrate Selection
The choice of substrate plays a crucial role. Materials such as plastics, metals, and paper have varying surface properties that impact how well UV inks bond. For example:
- Plastic Surfaces: Require pre-treatment for better adhesion.
- Metal Surfaces: Typically need a primer to ensure durability.
- Paper Surfaces: Can naturally absorb inks, affecting adhesion levels.
2. Surface Energy
The surface energy of a substrate affects how UV inks spread on its surface. Higher surface energy can enhance adhesion, while lower surface energy may lead to issues such as beading of the ink, resulting in poor bonding.
3. Pre-Treatment Methods
Implementing pre-treatment techniques can significantly enhance UV ink adhesion. Common methods include:
- Corona Treatment: Increases surface energy by oxidizing the surface.
- Flame Treatment: Similar to corona but utilizes an open flame to achieve higher adhesion.
- Chemical Treatment: Involves using specific chemicals to modify the substrate surface.
4. Printing Conditions
Environmental factors such as temperature and humidity can also impact UV ink adhesion. Optimal conditions usually yield better results. It’s important to maintain controlled settings to minimize variables that could affect the curing process.
Enhancing UV Ink Adhesion: Best Practices
To achieve and maintain excellent adhesion, printers can implement several best practices:
- Choose the Right Ink: Not all UV inks are created equal. Selecting inks that are specifically formulated for the intended substrate can lead to better adhesion.
- Optimize Printing Speed: Finding the right balance between printing speed and curing time is crucial. Slower speeds may enhance adhesion as they allow more time for the ink to bond.
- Maintain Ink Viscosity: The viscosity of the ink affects how it reacts during the curing process. Regularly checking and adjusting the viscosity can help improve adhesion.
- Use Proper Curing Equipment: Ensure that UV lamps are in good condition and appropriate for the specific inks being used. Regular maintenance of curing units is essential.
Challenges in Achieving Optimal UV Ink Adhesion
Despite advancements in technology and materials, printers often face challenges in achieving optimal adhesion:
1. Substrate Variability
Differences in texture, coatings, and inherent properties of various substrates can lead to inconsistencies in adhesion.
2. Environmental Conditions
External factors such as temperature fluctuations and humidity levels can impact curing and adhesion, making it essential to monitor environmental conditions closely.
3. Inadequate Curing
Under or over-curing UV inks can be detrimental. Insufficient curing leads to poor adhesion, while excessive curing can make inks brittle and prone to chipping.
Case Studies: Successful Implementation of UV Ink Adhesion
Examining successful case studies can provide insights into effective practices for improving UV ink adhesion:
Case Study 1: Plastic Retail Packaging
A company producing plastic retail packages faced challenges with ink adherence that led to surface scuffing. By implementing corona treatment and selecting a high-performance UV ink, they significantly improved adhesion, resulting in a 30% decrease in rejected products due to adhesion failures.
Case Study 2: Metal Business Cards
A print service specializing in metal business cards utilized chemical pre-treatment methods before applying UV ink. This ensured strong adhesion, and the durability of the prints improved tenfold, leading to increased customer satisfaction and repeat business.
The Future of UV Ink Adhesion in Printing Services
As technology evolves, the future of UV ink adhesion looks promising. Innovations in ink formulations, pre-treatment techniques, and curing technologies are set to enhance the overall adhesion performance. Some trends to watch for include:
- Eco-Friendly Inks: The rise of environmentally friendly UV inks that offer similar performance while being less harmful to the environment.
- Advanced Curing Technologies: The development of new UV curing systems that provide more even and adjustable curing options.
- Smart Printing Solutions: Integration of IoT and AI technologies for real-time monitoring of printing and curing conditions to optimize results continually.
In conclusion, mastering UV ink adhesion is vital for producing high-quality, durable printed materials. By understanding the factors that affect adhesion and implementing best practices, businesses can enhance their printing services, ensuring superior outcomes for their customers.
For more information on exceptional printing services and to explore capabilities in UV ink adhesion, visit bostonindustrialsolutions.com.